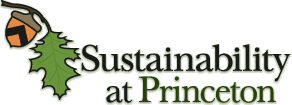
Streicker Bridge in Office of Sustainability's Green Tour
See video >
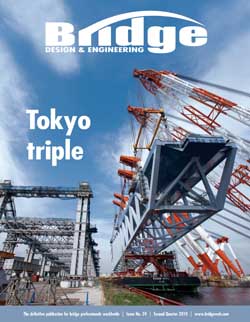
Streicker Bridge in "Bridge design & eng."
Read more >
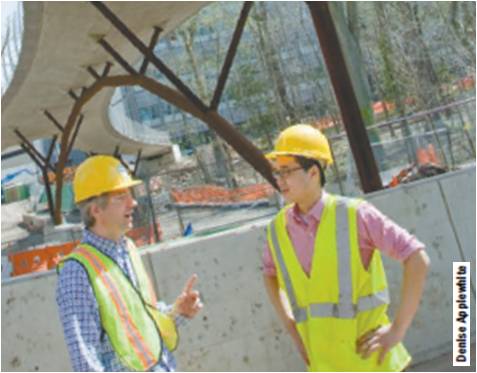
Senior thesis on Streicker Bridge in PU Bulletin >
|
Structural Health Monitoring of Streicker Bridge |
|
The Streicker Bridge is a new pedestrian bridge built at Princeton University campus, over the busy Washington Road. Besides its primary aim, to provide and facilitate safe pedestrian crossing over the Washington Road, the bridge has strong symbolic and aesthetic significance. Created as a part of Princeton University’s Natural Sciences neighborhood, the bridge connects the Icahn Laboratory (Lewis-Sigler Institute for Integrative Genomics) and new neuroscience and psychology building (under design) on the west with Jadwin Hall (physics), new Chemistry building, and Lewis library on the east. The bridge will “stand as a tangible symbol of the cross-disciplinary collaborations that are central to scientific research and teaching today” (President S.M. Tilghman in News at Princeton 2006). The bridge’s “X” shape in plane symbolizes these cross-disciplinary collaborations, and the arch itself represents the south entrance gate to Princeton Campus.
The bridge was funded by John Harrison Streicker (Princeton class 1964) and overall design was made by world renowned Swiss bridge designer Christian Menn. Detailed design was performed by HNTB Corporation’s Theodore Zoli (Princeton class 1988) and Ryan Woodward (Princeton class 2002). Turner Construction Company was the main contractor. Supervision and coordination has been carried out by the representatives from the Office of Design and Construction of Princeton University.
The Streicker Bridge has a main span and four approaching ramps, so-called legs. Structurally, the main span is a deck-stiffened arch and the legs are curved continuous girders supported by steel columns. The legs are horizontally curved and the shape of the main span follows this curvature. The arch and columns are weathering steel while the main deck and legs is reinforced post-tensioned concrete. Photographs of the bridge under construction are given in Figures 1 and 2, as well as in the header of this page. |
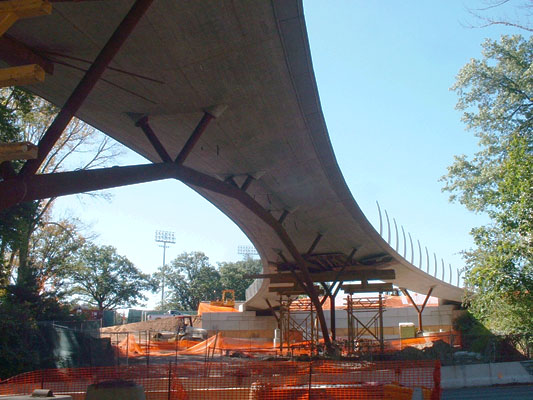
Fig. 1: Streicker Bridge, view from below.
|
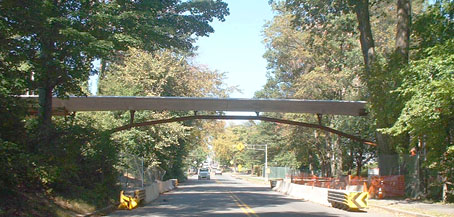
Fig. 2: Streicker Bridge, view from south. |
SHM Lab at Princeton University instrumented the bridge with various SHM systems, in order to use it as an on-site laboratory for short- and long-term research and educational purposes. The research will focus on addressing some of general SHM challenges as well as research in domain of monitoring approaches, methods, and instrumentation. The SHM of Streicker Bridge will serve as a support to university course on SHM and several other courses related to structural analysis and design. Briefly, the SHM of Streicker Bridge will address: |
General SHM challenges: (1) Bridge education gap, (2) Collect real structural behavior data set, (3) Identify changes in strain patterns caused by unusual behaviors, (4) Characterize the SHM contribution to sustainability of built environment;
R&D in domain of monitoring methods: (A) Assess performances of fiber optic methods for deck-stiffened arch and curved continuous girder; (B) Detect unusual structural behavior based on dynamic strain and curvature monitoring, (C) Determine the influence of concentrated load to the measurement of long-gauge sensor;
R&D in domain of instrumentation: (I) Compare performances of various monitoring systems, (II) Test newly developed sensors and monitoring components;
SHM related to Streicker Bridge itself: (a) Verify the design, (b) Monitor long-term performance of the bridge, (c) Demonstrate long-term monitoring benefits; |
 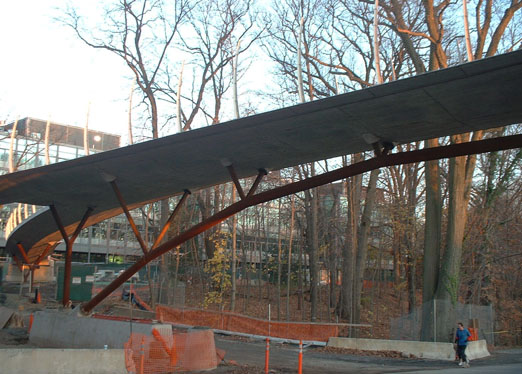
Fig. 3: View to monitored half of main span and south-east leg.
|
Support to teaching and outreach activities: Offer a source for (i) future senior theses, (ii) CEE 509/510: Directed research / Research seminar papers, and (iii) CEE 539: Special Topics in MMS – SHM: course projects and hands on experience; (iv) Give a tangible demonstration for students in CEE 312: Statics of structures, (v) Facilitate outreach such as short courses on SHM for practitioners or demonstrations and visits for community members.
|
Scientific contributions. Monitoring results will increase knowledge basis concerning the real structural behavior and will help to build reliable algorithms for damage and performance degradation detection based on objective data. In addition, future sensing technologies and methods will be installed and tested on the bridge. The ability of SHM to improve long-term bridge management and decrease life-cycle costs will be evaluated along with SHM’s potential to contribute to the sustainability of built environment. The results may have the potential to impact several other fields of civil engineering such as numerical modeling, structural analysis, life-cycle performance, and materials science..
Educational contributions. The SHM of Streicker Bridge was instrumental in the newly introduced graduate course CEE 539 on SHM – students were involved in all phases of project including design of monitoring strategy, installation of the system, data handling, interpretation and analysis. An undergraduate student conducted his senior thesis within the project in 2010, and the others will follow. Beside the course on SHM, the instrumented bridge will be of great support to the other departmental and interdepartmental courses such as newly introduced CEE 312 Statics of Structures and ELE547C_S2010 Selected Topics in Solid-State Electronics: Large Area Electronics.
Broader impact. The Bridge itself has been transformed into a laboratory which will serve not only for scientific and courses purposes, but will also be used for demonstration purposes for K-12 students, public, policy makers (e.g. students of Woodrow Wilson School as future policy makers), and decision makers (e.g. departments of transportation – DOT). The SHM of Streicker Bridge will be integrated in Short Courses for practitioners - civil engineers, consultants, contractors, and owners of structures. Finally, the SHM will provide an increased level of safety for the bridge users and improved management for the bridge owner are expected.
|
The SHM of Streicker Bridge is a long-term project and it will be realized in several phases. The initial phase consisted of instrumentation of main span (completed on August 14, 2009) and south-east leg (completed on October 22, 2009) with the following two fiber-optic sensing technologies:
(1) Discrete Fiber Bragg-Grating (FBG) long-gage sensing technology (average strain and temperature measurements);
(2) Truly distributed sensing technology based on Brillouin Optical Time Domain Analysis (average strain and temperature measurements).
Fiber-optic sensing (FOS) technologies are used since the optical fibers feature high sensitivity, durability and long-term stability. The FBG long-gage sensors can monitor average strain, average shear strain, average curvature, deformed shape, and temperature in inhomogeneous materials such as concrete, and allows global structural monitoring in both static and high frequency dynamic mode. The BOTDA distributed sensors provide for average strain, integrity, and temperature monitoring. Each type sensor is interrogated with appropriate proven and reliable high-performance reading unit.
The sensors were embedded in concrete during the construction. Installation was performed by professor Glisic and the following students:
Undergradutate Students: Maryanne Wachter, Jessica Hsu, George Lederman, Jeremy Chen,
Graduate Students: Chienchuan Chen, Allison Halpern, David Hubbell, Morgan Neal, Daniel Reynolds, and Daniel Schiffner.
Visiting professor Ignacio Paya-Zaforteza participated in the installation and personnel from Turner Construction Company, Office of Design and Construction, and HNTB Corporation offered precious help. Photographs taken during the installation are presented in Figures 3 – 7. |
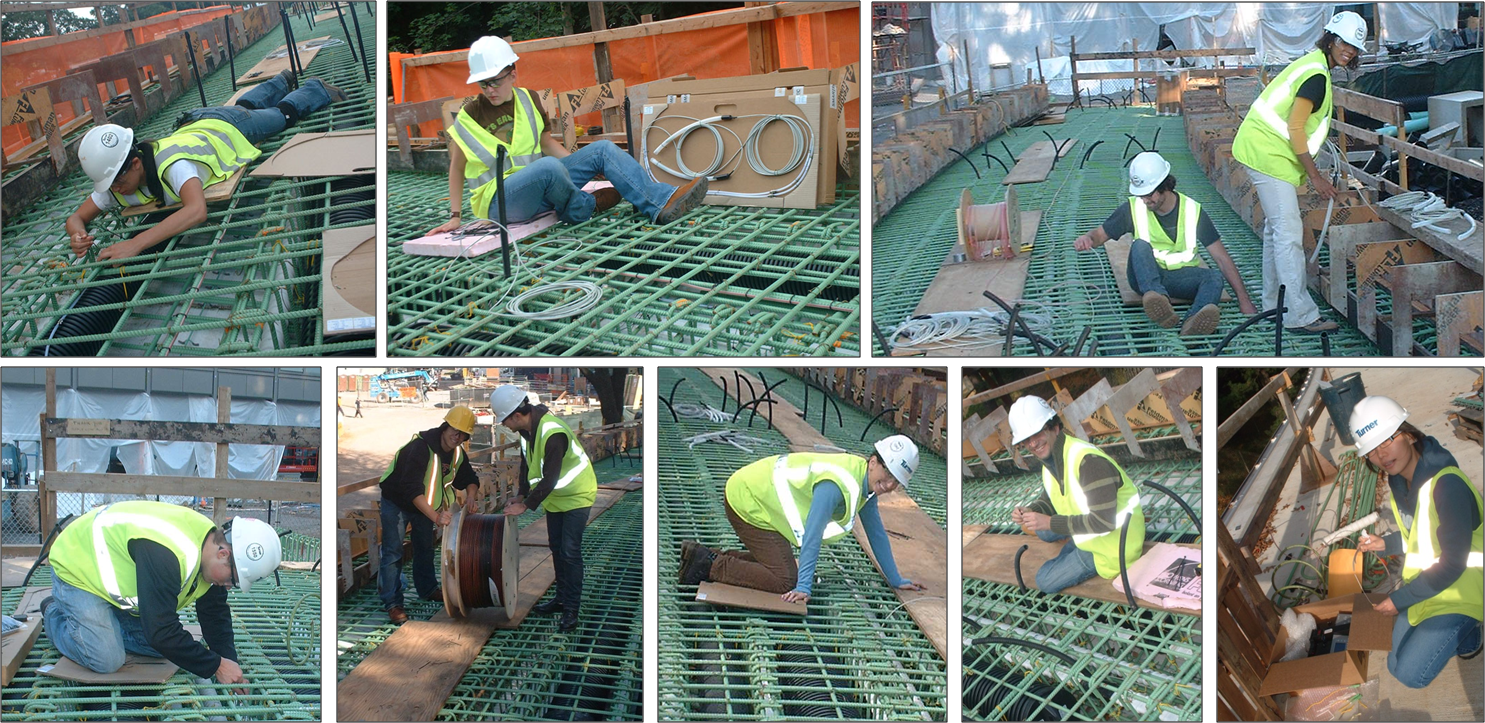
Fig. 4: Various phases of installation of FBG discrete long-gage sensors and BOTDA distributed sensors.
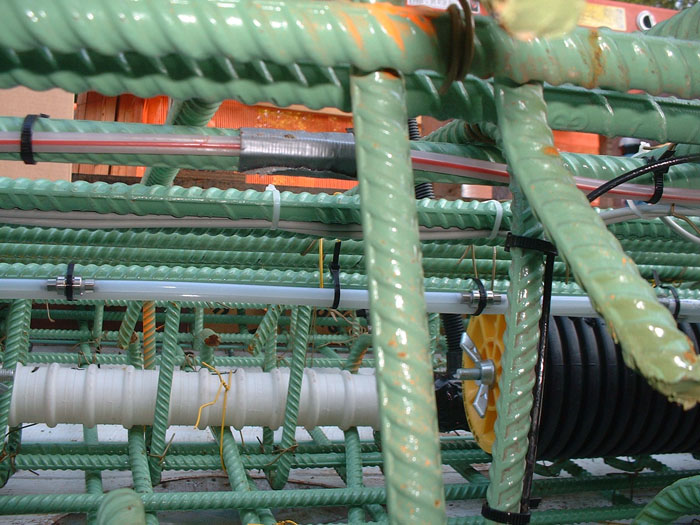  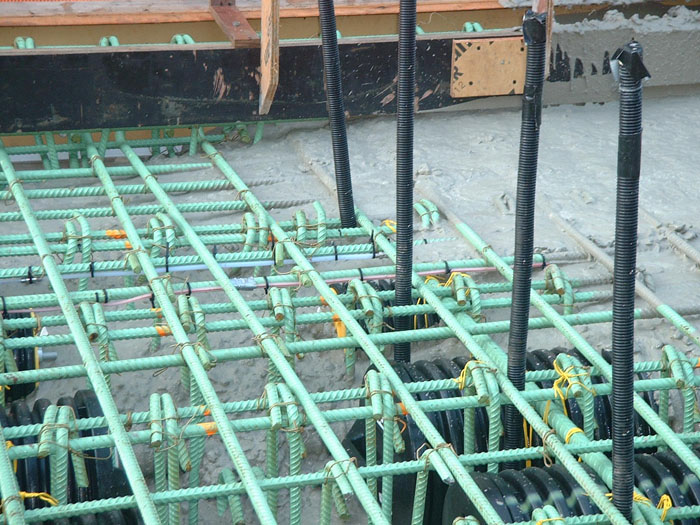  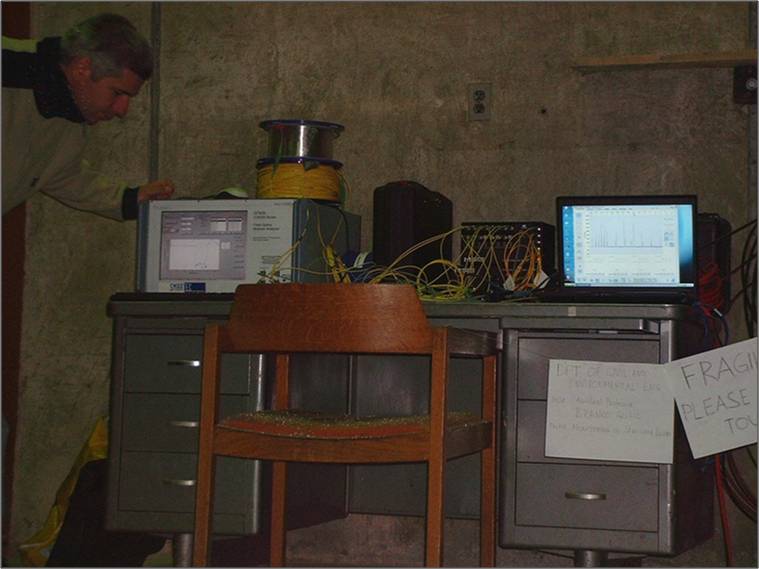
Fig. 5: Sensors of both types tied to rebars. Fig. 6: Pouring of concrete over sensors. Fig. 7: Temporary central measurement point. |
The first two weeks of monitoring performed on the main span included early age deformation of concrete (pouring of concrete was performed on August 15, 2009) and post-tensioning deformation (performed on August 21, 2009). An example of the data recorded by discrete FBG long-gage sensors is given in Figures 8 – 9. |
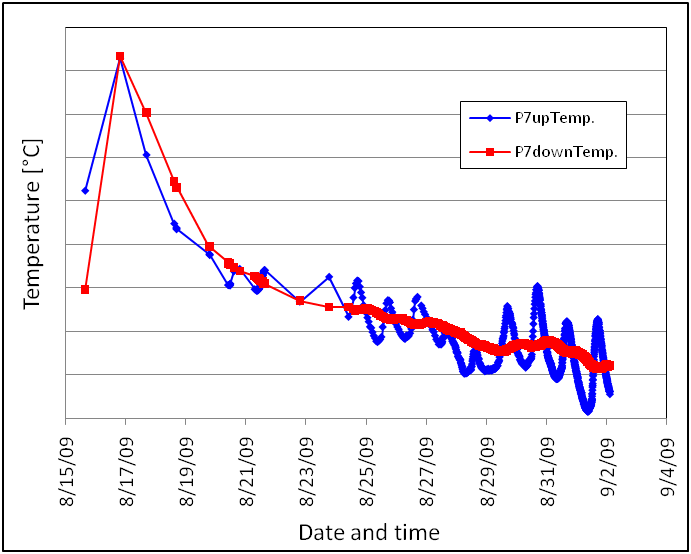
Figure 8: Evolution of temperature in points close to top (up) and bottom (down) of the cross-section above column P7. |
|
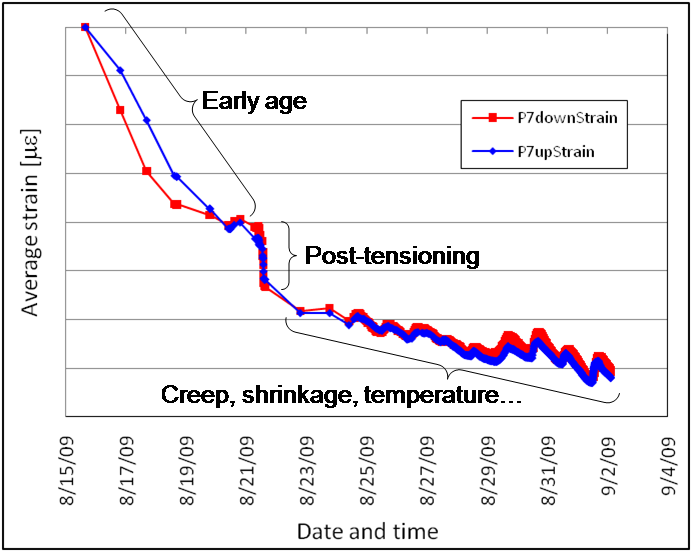
Figure 9: Evolution of average strain in points close to top (up) and bottom (down) of the cross-section above column P7. |
|
An example of unprocessed results obtained from distributed BOTDA sensor installed in south-east leg is given in Figure 10. The diagram shows the change in strain due to post-tensioning of the girder.
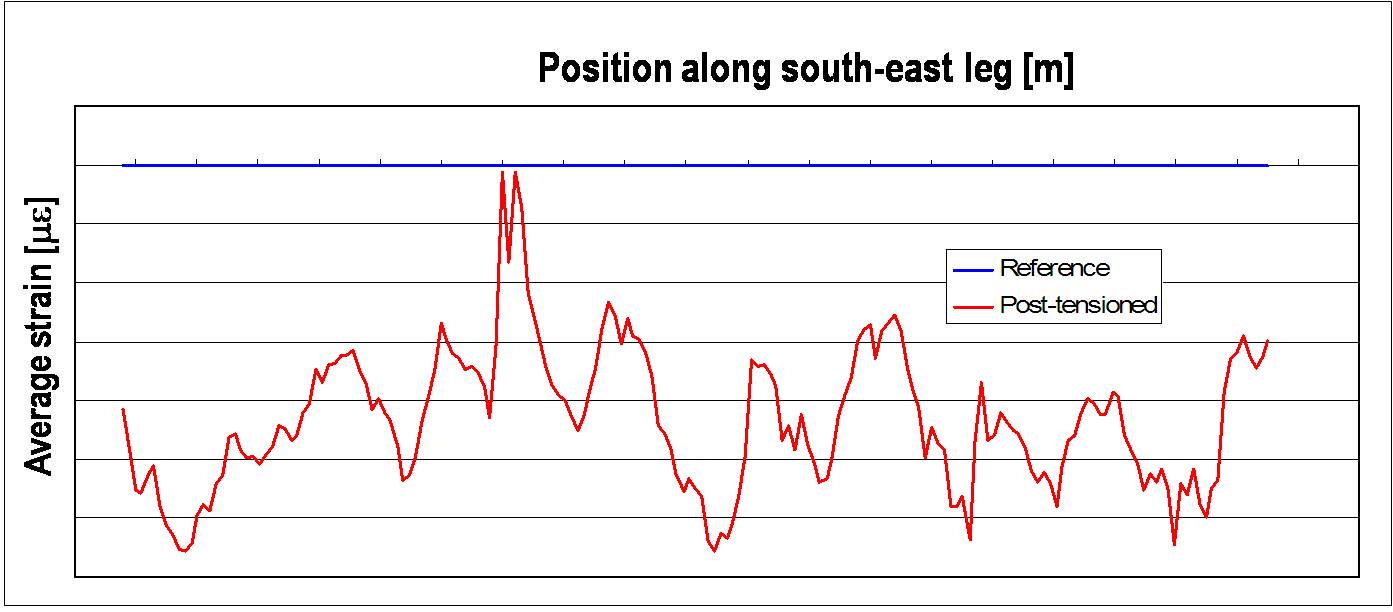
Figure 10: Unprocessed average strain measured by BOTDA sensor during post-tensioning of south-east leg. |
The analysis of results collected during the construction period incuding early age of concrete and post-tensioning is analysed by undergraduate student Kenneth Liew, graduate student Konstantinos-Nikolaos Bakis, and graduate students that participated in the installation and followed the course CEE 539 on SHM.
|
This project has been realized with important support, great help, and kind collaboration of several professionals and companies:
Steve Hancock and his construction team from Turner Construction Company, Somerset, NJ
Ryan Woodward and Ted Zoli, HNTB Corporation, New York, NY
Dong Lee and his team from A.G. Construction Corporation, Lincoln Park, NJ
Steven Mancini and Timothy R. Wintermute, Vollers Excavating & Construction, Inc., North Branch, NJ
SMARTEC SA, Switzerland
Micron Optics, Inc., Atlanta, GA
Geoffrey Gettelfinger, Physics Department, Princeton University
James P. Wallace and Miles Hersey, Office of Design and Construction, Princeton University
Shana Weber, Office of Sustainability, Princeton University
Paul Prucnal, Yanhua Deng, and Mable Fok, Department of Electrical Engineering, Princeton University
Faculty and staff of Department of Civil and Environmental Engineering, Princeton University
|
|
|
|
|